At Tillamook County Creamery Association (TCCA), we recognize that recycling and repurposing material offers economic and environmental benefits. It creates jobs, conserves natural resources, saves energy, saves water, reduces pollution, and reduces greenhouse gas emissions. At TCCA, not only do we recognize the value of these benefits, but we also remain committed to preventing and diverting waste because it is the right thing to do. As a farmer-owned cooperative and CPG company, we know that we have a responsibility to prevent food waste throughout the value chain.
“Waste Management and TCCA have a strong shared value that guides our partnership. We do the right thing the right way. We share a commitment to sustainability, recycling, and re-use in everything we do.”
-Daniel Vo, Account Manager, Waste Management
Stewardship Charter: At TCCA, we uphold our tradition of doing things right by committing to a business model rooted in Stewardship. In 2017, we established a board-approved, third-party reviewed Stewardship Charter that defines our vision and our framework. Our Charter is centered on commitments to six key stakeholders, which encompass the issues most important to our business: Thriving Farms, Healthful Cows, Inspired Consumers, Enduring Ecosystems, Fulfilled Employees and Enriched Communities.
We use our Stewardship Charter as the anchor of our Stewardship Management System; that is, we have policies, procedures, documentation, measurement and communication, which cascade from the Stewardship Charter and guide our decision making. Adopting a management system like this is intentional—it ensures we embed our Stewardship commitments across all business functions, not just within our Stewardship Team. It also holds us accountable to our farmers, consumers, suppliers, employees, customers and neighbors. Upholding our Stewardship Charter is one of our five company shared values and one of our four top-level business objectives, or time-bound goals.
One of our Stewardship Charter commitments is to Enduring Ecosystems. As part of this commitment, we strive to send zero waste to landfill in order to minimize our environmental impact. Our zero waste target and approach is in accordance with the Zero Waste International Alliance (ZWIA) definition of Zero Waste: we must achieve at least 90 percent diversion from landfills, incinerators and the environment, and commit to a goal of reducing the amount of materials discarded and any discards going to thermal processes. We have a direct influence over the production of our products and play a role in reducing waste generation in our value chain.
Materials Audit: Following the adage, “you cannot manage what you cannot measure,” we partnered with Community Environmental Services at Portland State University in 2017 to conduct a third-party materials audit of our production facilities. Their analysis included waste composition and diversion opportunities. This information has since been used to guide subsequent actions, serving as the foundation of our progress.
Materials Management Policy: Our commitment to zero waste to landfill is outlined and enforced through a company-wide Materials Management Policy. Our objective is to first minimize our generation of waste and, where source reduction is not possible, create value by diverting existing waste streams from the landfill. At a minimum, this means we practice compliance with local, state and federal laws for hazardous and non-hazardous waste disposal. Managing our waste in a manner that maintains a clean, safe and sanitary work environment has been a pre-requisite for doing business since day one. We enforce compliance through our internal Waste Management and Disposal Policy and Toxic Use and Hazardous Waste Reduction Policies. In 2019, we received no fines for environmental non-compliance.
Beyond compliance, we strive to adopt the following standards to achieve our objective:
The EPA Waste Management Hierarchy guidelines for material waste (Source Reduction & Reuse; Recycling / Composting; Energy Recovery; Treatment & Disposal); and,
The EPA Food Recovery Hierarchy guidelines for organic waste (Source Reduction; Feed Hungry People; Feed Animals; Industrial Uses; Composting; Landfill / Incineration).
Adherence to these guidelines helps us to achieve our objective in that we limit waste to landfill. However, we also recognize that no single waste management approach is suitable for each waste stream in every circumstance. Upholding these guidelines may have financial implications or require a re-evaluation of pre-existing commitments within a given municipality, or both. Consideration of any trade-offs will be evaluated on a case-by-case basis by the appropriate internal stakeholders.
Key Players: We know that we have the potential to generate waste at any stage along the lifecycle of our product, from milk production, to manufacturing, packaging, distribution and consumer use and disposal. We are, therefore, working to create a culture where all farmer-owners and employees are held accountable for reducing or diverting waste. In 2018, we formed two committees to meet our objective.
Waste Management Committee: Our cross-functional Waste Management Committee has employees representing multiple departments and all operating locations. They meet once a month and are tasked with five key responsibilities:
Champion ideas from respective work streams that would prevent or divert waste;
Conduct waste audit(s) and data analysis;
Prioritize projects, drive progress against program objective and targets;
Standardize receptacle signage across all sites, provide training for stakeholders; and,
Foster a culture of waste-awareness and continuous improvement.
Steering Committee: Our Waste Management Committee is sponsored by a Steering Committee of six leadership-level employees. This Steering Committee advocates for the efforts of the Waste Management Committee to ensure that projects receive leadership team and executive team support.
Key Performance Indicators: We present qualitative and quantitative information alongside our financials to our leadership team, executive team and board of directors. Our Operations, Farm Services and Environment and Community Impact teams regularly track company-wide waste generation (in pounds) and landfill diversion (in pounds). We include this waste data in our annual environmental footprint calculations (2012-2019). This includes the quantification of end-of-life impacts associated with packaging waste.
Awards and Recognition: In 2017, our Portland Outpost earned a Sustainability at Work Gold Certification. This certification recognizes our commitment to landfill diversion initiatives in our office space, including: recycled e-waste, reusable office dishware, proper recycling of fluorescent lights, reduced printing requirements and composting of food scraps.
The following sections detail specific efforts to manage and to reduce waste.
Our Engineering Department works to identify opportunities for improvement in operating facilities. One example is the opening of a joint venture whey processing facility in Boardman. During the cheese-make process, we make cheese curds and a sweet liquid called whey. Historically, this whey was discarded as “waste” because it was considered an unnecessary by-product. Recognizing an opportunity to increase value and reduce trucking of liquid whey, we formed a joint venture to build a new whey drying facility in Boardman. Our Engineering Department led the design and construction of a facility that separates and dries protein and lactose powders that can be used in various nutrition products and supplements—a significant reduction of processing waste.
Packaging plays an important role in protecting the quality and nutritional benefits of our products because it allows them to be stored, transported and used safely. A good package is the first step in preventing food waste. However, packaging also presents environmental challenges. It uses valuable resources and generates waste when not properly recycled or repurposed.
In research and development, we have a dedicated team of packaging engineers working exclusively to design and manufacture innovative and sustainable packaging for perishable products. This means we source recyclable, light-weight and low-volume materials where possible, without compromising the function, safety, quality and consumer perception of our products.
While we consider sustainable packaging criteria wherever applicable and feasible, we also know that an increase in packaging can sometimes reduce environmental impact because it prevents food waste—a major contributor to greenhouse gas emissions. We, therefore, commit to a holistic evaluation of our options to most effectively mitigate our environmental footprint. In 2019, we initiated our first-ever packaging life cycle analysis (LCA) to assess the environmental impact of our baseline ice cream pint packaging against multiple compostable options. We anticipate results in 2020.
We take a multi-pronged approach to fight food waste and feed those in need.
First, we strive to use resources efficiently and minimize any waste from going to landfill through reduction, repurposing, recycling, composting and energy-recovery efforts. At TCCA, we have a Continuous Improvement Team dedicated to eliminating material waste and inefficiencies in our manufacturing facilities. Over 50 percent of our employees have received Lean Six Sigma training. This means over half of our employee base is trained to think about waste management daily.
Assuming we cannot minimize waste, we next repurpose it by feeding people and animals when possible. We support the Oregon Food Bank, schools in Tillamook and Morrow Counties and other organizations by providing short-code product, or product that is safe and of high-quality but nearing its expiration date. Each year, we donate approximately $250,000 worth of short-code product to our communities. Product that is not safe for human consumption is donated to local non-dairy farmers. In 2019, we had over 200,000 pounds of cheese scrap donated to agricultural producers. It is also important to mention that roughly 30 percent of our dairy herd rations are comprised of high-quality agricultural by-products, such as soy meal, cotton seed and cannery corn. Because cows are ruminant animals, their digestive systems can process these nutritious by-products that humans cannot, which means this waste is prevented from otherwise going to landfill.
Assuming we cannot feed people or animals, we recycle and compost. In 2019, we diverted over 6,000 pounds of organic waste from the landfill through an employee-led composting program in our Portland Outpost. We send about 50 percent of our farmer-owner manure to three local biodigesters in Tillamook County. The biodigesters intake waste to generate roughly 700 kWh of energy each year, providing power for over 1,000 homes. This helps create energy independence for our local community.
Threemile Canyon Farms in eastern Oregon, which grew out of a milk supply relationship with Tillamook that began nearly 20 years ago, is an example of a partner who upholds our standards for environmental stewardship. Threemile Canyon Farms has created a closed-loop farm, which means the dairy and crop farms continually sustain and improve one another, so nothing goes to waste, not even cow manure. Cow manure is sent to an on-site methane digester that converts waste into clean, renewable natural gas. In addition to providing renewable power, it also provides nutrients that go back into crops, which in turn feeds the cows. Doing this also improves air quality. The digester sequesters around 136,000 metric tons per year of CO2-eq. This is equivalent to the annual greenhouse gas emissions from 28,875 passenger vehicles, or CO2-eq emissions from 16,285 homes’ energy consumption, or carbon sequestration by 160,061 acres of forest land.
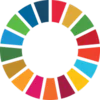
U.N. Sustainable Development Goals
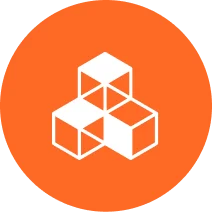
Goal 9
Build Resilient Infrastructure, Promote Sustainable Industrialization, and Foster Innovation
Adopting and supporting new technologies, such as the digesters, is just one way in which we are committed to advancing the industry through innovation.